Les travailleurs inactifs ou les matériaux inutilisés qui ne peuvent pas être recyclés ou réutilisés sont un frein à la productivité d'une entreprise. Cette mise en évidence de l'
élimination des déchets est le point de départ de l'idée du lean en tant que
système de gestion. Appelé
lean manufacturing ou
lean production, cette méthodologie peut être appliquée universellement. Les principes du lean manufacturing peuvent aider vos processus de métier à gagner en efficacité et, par conséquent, à devenir compétitifs sur n'importe quel marché. Suivez cet article pour plus de détails sur ce concept.
Qu’est-ce que le lean manufacturing ?
Objectif : réduire les déchets
Qui dit
travailler en tant qu'operateur de production dit lean manufacturing. En fait, le lean manufacturing est une méthodologie qui se concentre sur la
réduction des déchets dans les
systèmes de fabrication tout en maximisant simultanément la
productivité. Les déchets sont considérés comme tout ce que les clients ne croient pas avoir de valeur ajoutée et ne sont pas prêts à payer. Certains des avantages du lean manufacturing peuvent inclure des délais de livraison réduits, des coûts d'exploitation réduits et une meilleure qualité des produits.
Une technique de production
Le lean manufacturing, également connu sous le nom de production, est une pratique que les organisations de nombreux domaines peuvent utiliser. Parmi les entreprises bien connues qui utilisent le lean, à savoir Toyota, Intel, John Deere et Nike. Cette approche est basée sur le système de
production Toyota et est toujours utilisée par ces sociétés ainsi que par une myriade d'autres. Les entreprises qui utilisent la planification des ressources d'entreprise peuvent également bénéficier d'un
système de production allégé.
[caption id="attachment_2520" align="alignnone" width="745"]
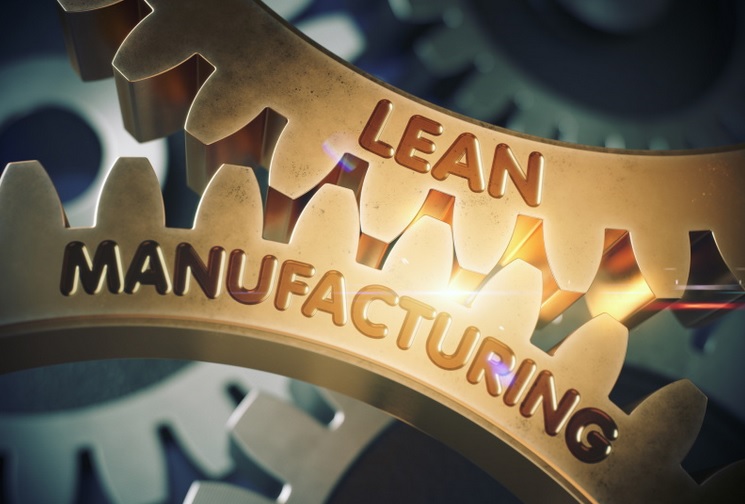
Découvrez l'histoire et les enjeux du lean manufacturing[/caption]
Histoire du lean manufacturing
L'idée de production allégée a été défendue pour la première fois par le système de production Toyota et appelée lean dans les années 1990. Cela a coïncidé avec la croissance de Toyota d'une petite entreprise à l'un des vendeurs de véhicules automobiles les plus prospères au monde.
Qui a inventé le Lean Manufacturing ?
La naissance du Lean Manufacturing remonte aux années 1950, à la japonaise
Toyota Motor Corporation. L'ère post-Seconde Guerre mondiale a été une période de crise profonde pour le Japon, incapable de suivre les systèmes de production de masse qui s'étaient propagés avec le
fordisme.
La nécessité de faire plus avec moins et donc de
réduire les coûts tout en maintenant une productivité élevée a conduit à la naissance d'un nouveau modèle de
production industrielle plus flexible. Toyota s'est imposé dans l'industrie automobile de l'époque grâce au
Toyota Production System (TPS), une méthodologie innovante pour ces années, axée sur la réduction continue des déchets et sur la
simplification des processus pour créer plus de valeur ajoutée pour le client final, dont les rythmes de production.
En ce qui concerne le terme "Lean Production", sa première apparition remonte à 1988, lorsqu'il apparaît sur un article inventé par un ancien ingénieur de Toyota. Mais elle ne s'est généralisée qu'à la suite de la publication en 1990 d'un ouvrage qui étudiait l'avenir de l'industrie automobile en analysant le système de production Toyota en l'associant à la Lean Production.
Un concept qui remonte à Benjamin Franklin !
Mais le lean en tant qu'idée qui englobe la réduction des déchets remonte à
Benjamin Franklin, qui en a parlé dans son Poor Richard's Almanack. Il a noté qu'éviter les coûts inutiles pourrait être plus rentable que d'augmenter les ventes. Cette idée et d'autres concepts pertinents apparaissent dans son essai « The way to wealth ». L'idée est devenue ce que l'ingénieur en mécanique Frederick Winslow Taylor a appelé la gestion scientifique, qui analyse et synthétise le flux de travail pour améliorer l'efficacité. Le terme lean manufacturing comme
principe de fabrication a été utilisé pour la première fois par l’ingénieur qualité chez Toyota John Krafcik.
Objectifs et stratégies du Lean Manufacturing
Réduire le gaspillage
Réduire ou éliminer le gaspillage est essentiel pour une gestion de projets allégée, mais les fins qu'elle sert peuvent être différentes selon la personne interrogée. Certains disent que le lean manufacturing augmente les bénéfices de l'entreprise tandis que d'autres maintiennent que ses améliorations sont uniquement bénéfiques pour le client. Mais existe quelques objectifs communs. D’abord, l’amélioration de la qualité. En effet, pour rester compétitives, les entreprises ne peuvent pas se montrer complaisantes, mais doivent répondre aux besoins et aux désirs changeants des clients. Par conséquent, les processus doivent être conçus pour répondre à leurs attentes et exigences. L'adoption d'une gestion de la qualité totale peut faire de l'amélioration de la qualité une priorité.
Éliminer les déchets
Ensuite, l’élimination des déchets. Ces derniers sont mauvais pour les coûts, les délais et les ressources. Après, la
réduction du temps. Le temps, c'est de l'argent, comme le dit l'adage, et perdre du temps, c'est donc perdre de l'argent. Réduire le temps nécessaire pour démarrer et terminer un projet vont créer de la valeur en augmentant l'efficacité. Apprenez et appliquez des stratégies de
gestion du temps. Enfin, la réduction des coûts totaux de l'argent est économisée lorsqu'une entreprise ne perd pas de temps, de matériel et de personnel sur des activités inutiles. La surproduction augmente également les coûts de stockage et d'entreposage. Comprendre la triple contrainte la première étape pour comprendre la
gestion des coûts.
Comment pratiquer le Lean Manufacturing ?
Le sens général du lean manufacturing est qu'il consiste en un ensemble d'outils qui aident à identifier et éliminer les déchets. Ces déchets peuvent être créés par une surcharge et une inégalité des
charges de travail. L'élimination des déchets de tout système améliore la qualité et le temps de production, tout en réduisant les coûts. Certains de ces outils incluent des cartes de contrôle pour vérifier les charges de travail et assurer une maintenance productive totale. Ils améliorent ainsi l'intégrité et la qualité du
processus de fabrication.
Par ailleurs, une autre façon d'aborder la fabrication sans gaspillage est appelée Toyota Way, telle qu'elle a été développée par l'entreprise. Ici, l'accent est mis sur l'amélioration du flux de travail pour éliminer les irrégularités plutôt que le
gaspillage. Kanban est essentiel pour ce type de lean management. Ce ne sont là que des exemples, mais il en existe encore d’autres.
Les cinq principes du Lean Manufacturing
Le Lean Manufacturing repose sur cinq fondements qui, s'ils sont acceptés, contribuent à changer radicalement la façon de penser de l'entreprise.
- Valeur : le concept de valeur doit être pensé et cartographié du point de vue du client, de manière à engager un processus de correction des activités qui ne contribuent pas à sa création. Il faut préciser que quand on parle de valeur, on entend ce que le client est prêt à payer et pour cette raison il est important de connaître ses besoins réels ou latents. Il existe plusieurs techniques qualitatives et quantitatives pour savoir ce que veulent les clients, comment ils aimeraient que le produit soit livré et quel prix ils sont prêts à payer. Les plus courants sont les entretiens, les enquêtes, les informations démographiques et les analyses Web.
- Cartographie des activités créatrices de valeur : à partir de la valeur pour le client comme point de référence, toutes les activités qui contribuent à sa création peuvent être identifiées. Dans ce processus, deux types de déchets seront également identifiés : les activités sans valeur ajoutée mais nécessaires (à réduire au maximum) et les activités sans valeur et inutiles (à éliminer).
- Optimiser les processus de création de valeur : L'étape suivante consiste à maximiser les activités de création de valeur, en en faisant un flux continu pour garantir que le processus se déroule sans interruption. Pour cela, il peut être nécessaire de revoir l'organisation du travail, les équipements à utiliser pour faciliter la production, ou de repenser l'agencement de production.
- Système pull : la production n'est lancée que lorsqu'il y a une demande du client, puisque c'est le client qui "tire" la production, exactement ce que le client veut est produit avec la certitude de vendre. Cela vous permet de réduire les niveaux de stock et de limiter les stocks, considérés comme l'un des plus gros gaspillages de la fabrication, tout en garantissant que les matériaux sont toujours disponibles pour un flux de travail fluide. En conséquence, la liquidité augmente et améliore toute la gestion de l'entreprise.
- Amélioration : une fois franchies les quatre étapes précédentes qui visent à réduire les déchets, un processus d'amélioration de la production peut être lancé pour viser la perfection selon la philosophie Kaizen. À cette étape, la pensée Lean et l'amélioration continue des processus font partie de la culture organisationnelle.
Les avantages du Lean Manufacturing
Le principal avantage du Lean Manufacturing est qu'il permet de produire mieux en utilisant
moins de ressources. En minimisant les déchets et en recherchant la qualité totale, la création de valeur augmente également.
L'amélioration s'étend à toute l'entreprise, car adopter une méthodologie de production Lean nécessite un changement radical de la philosophie de l'entreprise. Basée sur un système tiré qui part de la demande du client, la production est proportionnée à cette demande réelle, tout comme les activités, les équipements, les machines et les espaces. En conséquence, la production devient efficace et efficiente, car la production excessive et les surcharges de travail sont éliminées et le temps consacré aux processus qui n'ajoutent pas de valeur est réduit.
Les changements dans la planification, la production et la gestion de la qualité ont également un effet positif sur l'emploi des personnes, la communication et la coopération au sein de l'entreprise.
[embed]https://www.youtube.com/watch?v=Ov8o8ACo4OM[/embed]